TECHNIQUE AND PROCESS
The basic raw material for this craft is shoal, pith which grows in abundance in marshy areas. The plant grows to a height of 5 to 6 ft. and the diameter of its stem is about 2 to 3 inches. Two types of shoal can be found in Bangladesh: Kath shoal which is hard and bhat shoal / Bhatua, which is soft and light. The latter is procured in the winter and dried in the sun. Other materials required for joining and decorating the pith are bamboo pieces, coloured paper, gold and silver thread, foil, clay, jute, yarn, paints of various colours, cotton waste, pieces of wood, jute sticks, and glue made from tamarind seeds.
For making objects from shoal, the artisan uses traditional and very basic tools. The main tool is the kaitha a sharp, thin piece of wood or stone that is used to cut or slice shoal. Specially prepared glues are used by the artisans which not only bind the shoal but protect it from various insects. The base for the glue is made by soaking tamarind seeds for three days and then drying and heating them on an open fire. The seeds are husked to separate the skin from the pulp. This mixture is then soaked for a week, strained and ground into a paste. After it is dry it is kept in a covered clay pot. Whenever needed a little tamarind flour is mixed with water to prepare the glue.
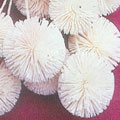
Skill evolved from generations of experience and tradition converts a piece of pith into an artistic object. The inner white part of the bark is the raw material used to produce a variety of forms for which four elementary processes are used.
Shola is cut into shapes of different sizes that are joined together to make figures, crowns/ mukut for the bride and groom, head dress/ topor for the groom , a cover for the brow/ kopali, toys, dolls, garlands, masks, flowers, such as Kadam phul, birds, animals, decorations for the home and other objects.
Thin slices of shoal are joined together to create a canvas for painting on with water colors on the occasion of various festivals.
With the help of clay moulds of various designs shoal pieces are molded into replicas of ornaments for clay idols, vines and leaves for decoration, of animal shapes such as monkey, bird, elephant, horse, boat, palanquin and cage.
For specific religious festivals, shoal is shaped into Durga mandali, Lakshmi Mandali, Manasa mandali and Trinath mandali. The latter festival has particular significance for shoal craftsmanship, since the seat of the god is occupied by the Shola mandali.
LOCATION
The main castes of shoal artisans are the Malakars, Pals and Acharyas. The artisans live and work in Keraniganj, Manikganj, Munshiganj, Comilla, Brahmanbaria, Kishoreganj, Netrakona, Moulavi Bazar, Habiganj, Sunamganj Jamalpur, Sherpur, Jessore, Magura, Khulna, Kushtia Rangpur, Chilmari, Syedpur and Southern Barisal.