Sholapith/ Pith/ Aeschynomene Indica/ Netti is derived from a reed which is pure white in colour and is exposed when the outer layer of the stalk is shaved. The core is light, porous, soft, and pliable and can be shaped to suit the imagination of the artisan. Dextrous hands shape this reed into many objects: scaled down models of temples, churches and mosques, carved images of Durga during puja time in Bengal, marriage headgear, flowers and garlands, toys and mobiles are all crafted from this reed.
PROCESS, TOOLS, AND TECHNIQUE
The pith plant is recognised by the shallow layer of leaves that float on the marshy water at a depth of two to six feet. The pith collector wades into the water to collect this reed, which is then dried thoroughly and sold as sticks in lengths of two to three feet. In Rajamundry district in Andhra Pradesh, for instance rate is Rs. 5 for a stick two feet in size. Good quality pith is pure white and smooth with a soft bark and no nodes, while poor quality pith is one where the core is reddish with a hard bark and has many nodes. The best time for the collection of pith is between the months of December and February.
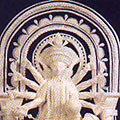
The tools used are simple and comprise of a knife, scissors, and geometry box. In West Bengal the iron knife called kath, is used to shave the outer cover of the stalk, so that the white core is exposed. This stalk can be shaved further into thin or thick sheets and shaped with a knife or scissors. The parts used to make various figures are glued together. The raw tendrils of the reed are boiled, ground and mixed with flour to make the glue paste. Once the flat sheets are made, a dozen of these can be tied tight at one end and cut into pieces to create various shapes, geometrical and floral. Artisans spend months on a piece, meticulously carving out the details. No part of the pith is wasted and leftover bits are used for making flowers, birds, and animal figures. The colouring on the finished product, if required, is done with bright coloured paint. Artisans from Tamil Nadu even make model townships for use by government officials; their replicas of temples, churches, mosques and buildings of architectural beauty are complete to the smallest detail.
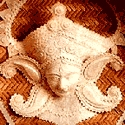
PRACTITIONERS AND LOCATION
Ezhilvighi, a State Awardee and Master Craftswoman from Thanjavur, Tamil Nadu, who has been practising this craft for about 17 years says: 'We take special orders from ministers, collectors and other government officials and film actors to make special designs for them. We have even made a wedding card for Vijaykanth, a leading Tamil actor.' J. Jayalalitha, Chief Minister of Tamil Nadu commissioned Ezhilvighi to make a model village, coloured realistically, with all amenities in place.
Ezhilvighi teaches this craft to women in rural areas in Tamil Nadu, so that they use the time productively and earn an income for themselves. She takes about a day for small figures, three days for a medium-sized Taj Mahal and upto 10 days for a big size Ganesha. After the figure is ready, it is enclosed in a glass case for safety and display. She cuts the glass herself and the glass is fixed on a plastic base, on which the figure rests. Her husband makes a yearly purchase of dry pith sticks from Rajamundry in Andhra Pradesh. 'The pith that grows there is of very good quality. They dry it and sell it to us. I buy a stock of 10,000 sticks, at Rs 5 for a 2 feet stick, on a yearly basis.'
In Tamil Nadu the craft flourishes in pockets of Thanjavur, Karaikkal, Tiruchirapalli, Nagapattinam, Pudukottai and in the Union Territory of Pondicherry. Here entire families are engaged in the craft.

In West Bengal, the artisans who craft works of art from the Shola are called Malakars and they claim their descent from Vishwakarma. However in one of the mythological tales of the malakars the origin of shoal crafts and the malakars is ascribed to Lord Shiva. As the legend goes Lord Shiva decided to adorn himself with a pure white mukut /crown and garland at his wedding with Gauri, the daughter of the Himalaya. But Lord Visvakarma, the creator of all craftsmen, did not know what material to use. In exasperation, Shiva threw a lock of hair into the pond. From this sprouted a water plant - the Bhat shoal.
Again Vishwakarma was hesitant, since he said he could carve only hard material such as wood or stone, but could not work with soft, fragile material. This time Shiva plucked a hair from his arm and threw it into the water. There emerged a handsome, young man, who was ordered to make the wedding mukut /crown, mala /garland and ornaments. He was a Malakar. It was thus ordained that at all weddings, the bride and groom should be adorned with shola decorations made by a Malakar. Because of this origin the Malakars do not owe their origin to Vishwakarma, but to Shiva.
Sholapith items form an integral part of the major religious rituals in West Bengal. Fine examples of craftsmanship can be seen during the Durga Puja celebrations. Every community in each village, town, and city needs an image as fine as they can afford, so the craft flourishes there. Traditionally the artisans also craft ritual and decorative items like garlands, chandmalas (literally moon garlands with filigree discs linked into elaborate chains), conical topors, or the head dress worn by young boys during their naming ceremony and by bridegrooms, and the mukut worn by the bride.
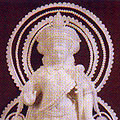
According to T. N. Mukherjee in his book Art Manufacturers of India that was compiled for the Glasgow International Exhibition in 1888, pith was worn by the aboriginal tribes as ear ornaments and colourful garlands of pith beads were used to decorate idols and were worn by brides and bridegrooms in Bengal.
On a recent meeting with Sholapith artisans from Dhubri, West Bengal, we noticed some very interesting changes in their craft products, the most amusing of which was the impact of films with Disney's characters, and Steven Spielberg's' Jurassic Park on the people of this little village. The artisan had created a shoal dinosaur, which was as popular among the children of the village, as the traditional magor mach or alligator, one of the toys that are sold all year round both in the village and in bigger towns and cities. Other changes that have taken place over the years are the use of chemical colours instead of the traditional vegetable dyes and the fact that the reed is purchased now instead of being collected by individual craftspersons.
An interesting feature of the sholapith is that it was the material used during British times for the production of the Sola Topi which was a necessary article of headwear for the British as protection from the hot mid-day sun of India. Shola products, when crafted, resemble ivory; however, unlike ivory they are brittle and break easily unless kept carefully. This ephemeral quality of the shoal gives it a precious quality.